In an internal combustion engine, the connecting rod is a critical component that facilitates the transfer of energy from the crankshaft to the piston. The crankshaft, located at the bottom of the engine, converts the reciprocating motion of the piston into rotary motion. The connecting rod, in turn, connects the crankshaft to the piston and enables the piston to move up and down within the engine's cylinder. As the crankshaft rotates, the connecting rod translates the rotary motion into linear motion, causing the piston to move up and down the cylinder. This up-and-down motion of the piston is essential for the engine's operation, as it allows for the intake of air and fuel into the cylinder, the compression of the air-fuel mixture, and the subsequent combustion and expansion of the gases.
The connecting rod plays a crucial role in the engine's performance and efficiency. It must be strong enough to withstand the high forces and stresses generated during engine operation, yet lightweight enough to minimize reciprocating mass and reduce engine vibration. The connecting rod's design and materials are carefully engineered to optimize its strength, durability, and weight characteristics.
The development of the connecting rod has played a significant role in the evolution of internal combustion engines. Early engines used simple connecting rods made of wrought iron or cast iron, but as engine speeds and power outputs increased, the need for stronger and more durable connecting rods became apparent. Today, connecting rods are typically forged from high-strength steel alloys or aluminum alloys, providing excellent strength-to-weight ratios and enhanced reliability. The design and manufacturing processes of connecting rods have also evolved over time, with advanced techniques such as powder metallurgy and precision machining enabling the production of complex shapes and tight tolerances.
The Connecting Rod
The connecting rod is a critical component in an internal combustion engine, responsible for transferring energy from the crankshaft to the piston. This essential function is achieved through several key aspects:
- Conversion: Transforms rotary motion of the crankshaft into linear motion of the piston.
- Force Transmission: Transfers the force generated by the crankshaft to the piston.
- Strength: Withstands high forces and stresses during engine operation.
- Durability: Ensures longevity and reliability under demanding engine conditions.
- Weight Optimization: Minimizes reciprocating mass to reduce engine vibration and improve efficiency.
- Precision: Manufactured with tight tolerances to ensure smooth and efficient operation.
- Materials: Typically forged from high-strength steel alloys or aluminum alloys for optimal strength-to-weight ratio.
These key aspects work in conjunction to enable the connecting rod to fulfill its crucial role in the engine. The conversion of rotary to linear motion is fundamental to the engine's operation, while force transmission ensures that the power generated by the crankshaft is effectively utilized. The strength and durability of the connecting rod are essential for handling the high forces and stresses encountered during combustion, while weight optimization and precision contribute to overall engine efficiency and performance. The choice of materials, often high-strength steel alloys or aluminum alloys, further enhances the connecting rod's ability to withstand the demanding conditions within an internal combustion engine.
1. Conversion
The conversion of rotary motion to linear motion is a fundamental aspect of the connecting rod's function in transferring energy from the crankshaft to the piston. This conversion is achieved through the connecting rod's unique design and its interaction with the crankshaft and piston.
- Crank Journal and Piston Pin: The connecting rod has two ends: the crank journal end, which connects to the crankshaft, and the piston pin end, which connects to the piston. The crank journal is a bearing surface that allows the connecting rod to rotate on the crankshaft, while the piston pin is a cylindrical pin that allows the connecting rod to pivot on the piston.
- Conversion Mechanism: As the crankshaft rotates, the crank journal causes the connecting rod to rotate about its axis. This rotation, in turn, causes the piston pin end of the connecting rod to move up and down, translating the crankshaft's rotary motion into the piston's linear motion.
- Power Transmission: The connecting rod's conversion of rotary to linear motion enables the transfer of force from the crankshaft to the piston. As the crankshaft rotates and the connecting rod translates this motion, the force generated by the crankshaft is transmitted to the piston, driving its up-and-down movement within the engine's cylinder.
The conversion of rotary to linear motion is essential for the proper functioning of the internal combustion engine. It allows the crankshaft's rotational energy to be utilized to drive the piston's reciprocating motion, which is crucial for the intake, compression, combustion, and exhaust processes that occur within the engine's cylinders.
2. Force Transmission
The force transmission aspect of the connecting rod's function is intricately connected to the overall energy transfer process from the crankshaft to the piston. This force transmission is crucial for converting the crankshaft's rotational motion into the piston's reciprocating motion, which is essential for the proper functioning of the internal combustion engine.
- Facet 1: Conversion of Rotary Motion to Linear Force
The connecting rod's design enables it to convert the crankshaft's rotary motion into a linear force that drives the piston's up-and-down movement. As the crankshaft rotates, the connecting rod's crank journal end rotates about the crankshaft, while the piston pin end translates this motion into linear displacement of the piston within the cylinder.
- Facet 2: Piston Acceleration and Deceleration
The force transmitted by the connecting rod plays a critical role in accelerating and decelerating the piston during its motion. The connecting rod's angularity and the varying distance between the crank journal and piston pin throughout the engine cycle result in a complex force profile that governs the piston's acceleration and deceleration patterns.
- Facet 3: Power Delivery and Engine Efficiency
The effective transmission of force from the crankshaft to the piston is essential for delivering power to the engine. The connecting rod's strength and rigidity ensure that the force is transferred efficiently, minimizing energy losses and contributing to the overall efficiency of the engine.
- Facet 4: Connecting Rod Strength and Durability
The force transmission function of the connecting rod demands high strength and durability. The connecting rod must withstand the substantial forces generated during combustion and the reciprocating motion of the piston. Its design and material composition are carefully engineered to ensure reliability and longevity under these demanding conditions.
In summary, the force transmission aspect of the connecting rod's operation is a fundamental element in the energy transfer process from the crankshaft to the piston. It enables the conversion of rotary motion to linear force, governs piston acceleration and deceleration, contributes to power delivery and engine efficiency, and necessitates the use of strong and durable connecting rod designs.
3. Strength
The strength of the connecting rod is a critical factor in its ability to transfer energy from the crankshaft to the piston. The connecting rod is subjected to high forces and stresses during engine operation, including:
- Tensile forces: The connecting rod is stretched as the piston moves up the cylinder.
- Compressive forces: The connecting rod is compressed as the piston moves down the cylinder.
- Bending forces: The connecting rod is bent as the piston moves from side to side in the cylinder.
- Torsional forces: The connecting rod is twisted as the crankshaft rotates.
If the connecting rod is not strong enough to withstand these forces and stresses, it can fail, causing catastrophic engine damage.
The strength of the connecting rod is determined by its material composition, its design, and its manufacturing process. Connecting rods are typically made of high-strength steel alloys or aluminum alloys. The design of the connecting rod must take into account the forces and stresses that it will be subjected to. The manufacturing process must ensure that the connecting rod is properly heat-treated and finished to achieve the desired strength and durability.
The strength of the connecting rod is essential for the safe and efficient operation of an engine. A strong connecting rod will ensure that the energy from the crankshaft is transferred to the piston effectively, resulting in optimal engine performance.
4. Durability
The durability of the connecting rod is essential for the long-term performance and reliability of an engine. The connecting rod is subjected to high forces and stresses during engine operation, and it must be able to withstand these conditions without failing. If the connecting rod fails, it can cause catastrophic engine damage.
- Facet 1: Material composition
The material composition of the connecting rod is a key factor in its durability. Connecting rods are typically made of high-strength steel alloys or aluminum alloys. Steel alloys are strong and durable, but they are also heavy. Aluminum alloys are lighter than steel alloys, but they are not as strong. The choice of material depends on the specific application. For high-performance engines, steel alloys are typically used. For lightweight engines, aluminum alloys are typically used.
- Facet 2: Design
The design of the connecting rod also affects its durability. The connecting rod must be designed to withstand the forces and stresses that it will be subjected to. The design must take into account the material composition of the connecting rod, as well as the specific application. For example, a connecting rod for a high-performance engine will have a different design than a connecting rod for a lightweight engine.
- Facet 3: Manufacturing process
The manufacturing process also affects the durability of the connecting rod. The connecting rod must be properly heat-treated and finished to achieve the desired strength and durability. The manufacturing process must also ensure that the connecting rod is free of defects.
- Facet 4: Maintenance
The durability of the connecting rod can also be affected by maintenance. The connecting rod should be inspected regularly for signs of wear or damage. If the connecting rod is damaged, it should be replaced immediately.
By understanding the factors that affect the durability of the connecting rod, engineers can design and manufacture connecting rods that will provide long-term performance and reliability.
5. Weight Optimization
In the context of "the connecting rod transfers the energy of the crankshaft to the piston," weight optimization plays a crucial role in enhancing engine performance and efficiency. Reciprocating mass refers to the mass of components that move up and down within the engine, including the connecting rod, piston, and piston rings. Reducing this mass reduces the forces acting on the engine bearings and other components, leading to several benefits:
Reduced Engine Vibration: Lighter reciprocating components generate less vibration as they move. This reduction in vibration contributes to smoother engine operation, improving overall comfort and reducing noise levels.
Improved Engine Efficiency: Reducing reciprocating mass lowers the energy required to accelerate and decelerate these components. This translates to improved fuel economy and reduced emissions, as the engine can operate more efficiently.
Increased Power Output: Lighter reciprocating components allow the engine to rev more freely, resulting in increased power output. This is particularly beneficial in high-performance engines, where every ounce of power is crucial.
Weight optimization of the connecting rod is achieved through careful design and material selection. Engineers use lightweight materials such as aluminum alloys or titanium to reduce the mass of the connecting rod while maintaining its strength and durability. Advanced manufacturing techniques, such as forging and precision machining, enable the creation of complex shapes that optimize weight distribution and reduce stress concentrations.
In summary, weight optimization of the connecting rod, as a component of "the connecting rod transfers the energy of the crankshaft to the piston," is essential for improving engine performance, efficiency, and power output. By minimizing reciprocating mass, engineers can reduce engine vibration, improve fuel economy, and unleash the full potential of the engine.
6. Precision
In the context of "the connecting rod transfers the energy of the crankshaft to the piston," precision manufacturing plays a vital role in ensuring smooth and efficient engine operation. Precision refers to the ability to manufacture components with tight tolerances, minimizing variations in dimensions and ensuring a high degree of accuracy.
- Facet 1: Reduced Friction and Wear
Precisely manufactured connecting rods reduce friction between the piston pin and the crank journal. This reduction in friction minimizes wear and tear on these critical components, extending the lifespan of the engine and maintaining optimal performance.
- Facet 2: Optimized Combustion
Tight tolerances in the connecting rod's design ensure accurate piston movement within the cylinder. This precision contributes to proper combustion by maintaining the correct air-fuel mixture and preventing excessive blow-by, resulting in improved engine efficiency and power output.
- Facet 3: Reduced Noise and Vibration
Precision manufacturing minimizes imbalances and irregularities in the connecting rod's shape and weight. This reduction in manufacturing variability leads to smoother engine operation, reducing noise and vibration levels, and enhancing overall driving comfort.
- Facet 4: Reliability and Durability
Tight tolerances ensure consistent performance and reliability of the connecting rod. Precisely manufactured components are less prone to failure, reducing the risk of catastrophic engine damage and extending the engine's overall lifespan.
In conclusion, precision manufacturing of the connecting rod, as part of "the connecting rod transfers the energy of the crankshaft to the piston," is crucial for achieving smooth and efficient engine operation. By minimizing variations and maintaining tight tolerances, engineers can reduce friction, optimize combustion, and enhance the overall reliability and durability of the engine.
7. Materials
The materials used in the construction of connecting rods play a critical role in ensuring the efficient transfer of energy from the crankshaft to the piston. The selection of high-strength steel alloys or aluminum alloys for forging provides an optimal balance of strength and weight, enabling the connecting rod to withstand the demanding forces and stresses encountered during engine operation.
- Facet 1: Strength and Durability
The connecting rod is subjected to high tensile, compressive, bending, and torsional forces during engine operation. High-strength steel alloys, such as forged steel, offer exceptional strength-to-weight ratios, making them ideal for connecting rods that can endure these demanding conditions without failure or deformation.
- Facet 2: Weight Optimization
In the context of reciprocating engines, reducing the weight of the connecting rod is crucial for minimizing reciprocating mass. Aluminum alloys, known for their high strength-to-weight ratios, enable the production of lightweight connecting rods that contribute to improved engine efficiency, reduced vibrations, and increased power output.
- Facet 3: Wear Resistance
The connecting rod interfaces with the piston pin and crank journal, experiencing sliding contact and friction. Forged materials, such as steel alloys, provide excellent wear resistance, reducing the rate of wear and tear on these critical surfaces, ensuring long-term reliability and performance.
- Facet 4: Fatigue Resistance
Connecting rods are subjected to cyclic loading and unloading, which can lead to fatigue failure over time. High-strength steel alloys and aluminum alloys exhibit good fatigue resistance, enabling the connecting rod to withstand repeated stress cycles without compromising its structural integrity.
The careful selection and utilization of high-strength steel alloys or aluminum alloys in the forging process result in connecting rods that can effectively transfer energy from the crankshaft to the piston while maintaining their strength, durability, and weight optimization. These factors are essential for ensuring the overall efficiency, performance, and longevity of the internal combustion engine.
Frequently Asked Questions on "The Connecting Rod Transfers the Energy of the Crankshaft to the Piston"
This section addresses common questions and misconceptions surrounding the role and significance of the connecting rod in transferring energy within an internal combustion engine.
Question 1: What is the primary function of a connecting rod?
Answer: The connecting rod serves as a crucial intermediary between the crankshaft and the piston in an internal combustion engine. Its primary function is to transmit the reciprocating motion of the piston into rotary motion of the crankshaft, facilitating the conversion of energy within the engine.
Question 2: Why is the strength of the connecting rod important?
Answer: The connecting rod is subjected to significant forces during engine operation, including tensile, compressive, and bending forces. Its strength is paramount to ensure it can withstand these forces without failure or deformation, maintaining the integrity of the engine's operation.
Question 3: What are the key factors that determine the durability of a connecting rod?
Answer: The durability of a connecting rod is influenced by several factors, including the material composition, design, and manufacturing process. Choosing high-strength materials, employing robust designs, and adhering to precise manufacturing techniques contribute to the overall longevity and reliability of the connecting rod.
Question 4: How does the weight of the connecting rod affect engine performance?
Answer: The weight of the connecting rod is a crucial consideration in engine design. Lighter connecting rods reduce reciprocating mass, resulting in improved engine efficiency, reduced vibrations, and enhanced power output. Engineers strive to optimize the weight of the connecting rod while maintaining its strength and durability.
Question 5: What materials are commonly used in the construction of connecting rods?
Answer: Connecting rods are typically forged from high-strength steel alloys or aluminum alloys. Steel alloys offer exceptional strength-to-weight ratios, while aluminum alloys combine strength with lightness. The choice of material depends on the specific engine requirements and performance targets.
Question 6: How does precision manufacturing contribute to the efficiency of the connecting rod?
Answer: Precision manufacturing techniques ensure the connecting rod is produced with tight tolerances, minimizing variations in dimensions and ensuring high accuracy. This precision reduces friction between components, optimizes combustion, and enhances the overall efficiency and reliability of the connecting rod.
In summary, the connecting rod plays a vital role in transferring energy within an internal combustion engine. Its strength, durability, weight, material composition, and precision manufacturing are critical factors that influence its performance and the overall efficiency of the engine.
Transition to the next article section: Understanding the complexities of the connecting rod's function and the factors affecting its performance is essential for appreciating the intricate workings of an internal combustion engine.
Tips on Understanding "The Connecting Rod Transfers the Energy of the Crankshaft to the Piston"
To gain a comprehensive understanding of the connecting rod's function in transferring energy within an internal combustion engine, consider the following tips:
Tip 1: Grasp the Basic MechanismRecognize that the connecting rod serves as a crucial link between the crankshaft and piston, facilitating the conversion of reciprocating motion into rotary motion. This fundamental understanding provides the foundation for comprehending the connecting rod's significance.
Tip 2: Appreciate the Importance of StrengthComprehend the substantial forces acting upon the connecting rod during engine operation. Its strength is paramount to withstand these forces without failure, ensuring the integrity and smooth functioning of the engine.
Tip 3: Consider the Impact of DurabilityRecognize that a durable connecting rod ensures long-term reliability and performance. Factors such as material composition, design, and manufacturing processes influence its ability to endure demanding engine conditions.
Tip 4: Understand Weight OptimizationAppreciate the benefits of weight optimization in connecting rod design. Lighter connecting rods contribute to improved engine efficiency, reduced vibrations, and enhanced power output, highlighting the importance of weight considerations.
Tip 5: Explore Material ChoicesComprehend the significance of material selection for connecting rods. High-strength steel alloys and aluminum alloys offer unique advantages, and their suitability depends on specific engine requirements and performance targets.
Tip 6: Recognize the Role of Precision ManufacturingUnderstand the impact of precision manufacturing on connecting rod performance. Tight tolerances minimize friction, optimize combustion, and enhance overall efficiency and reliability, demonstrating the importance of precision in component production.
By incorporating these tips into your understanding, you can develop a comprehensive grasp of the connecting rod's function in transferring energy within an internal combustion engine.
Transition to the conclusion: A thorough understanding of the connecting rod's role is essential for appreciating the intricate workings of an internal combustion engine and its impact on overall performance and efficiency.
Conclusion
In conclusion, the connecting rod serves as a critical component in the internal combustion engine, facilitating the transfer of energy from the crankshaft to the piston. Its strength, durability, weight, material composition, and precision manufacturing are crucial factors that influence its performance and the overall efficiency of the engine.
Understanding the intricacies of the connecting rod's function provides valuable insights into the complex workings of an internal combustion engine. Engineers continuously strive to optimize connecting rod design and manufacturing techniques to enhance engine performance, efficiency, and reliability. As technology advances, the role of the connecting rod will continue to be pivotal in the development of cleaner, more efficient, and powerful internal combustion engines.
You Might Also Like
Find Your Dream Casting Calls With MyCastingFileDiscover The Perfect Fit! Try On Bras Virtually Now
The Ultimate Guide To Being A Mom: Everything You Need To Know About Parenting Timmy
Uncover The Unique Sounds Of The Zebra: What's Their Call?
Discover Victorian Charm: Unveiling Towanda, PA's Enchanting Victorian Charm Inn
Article Recommendations
- The World Of Theatrical Artists An Indepth Guide
- How To Access And Navigate The Senegence Distributor Login Portal
- Jacks Garage Your Goto Destination For Automotive Excellence
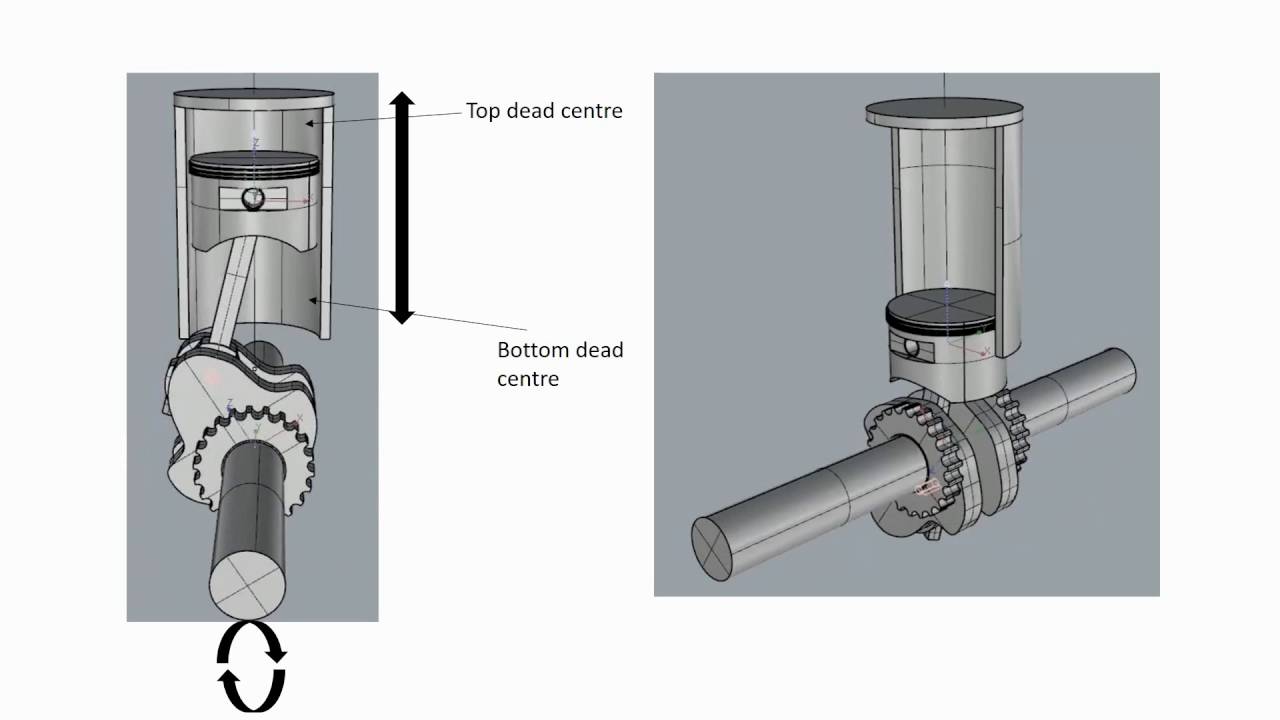

